Anilox cleaning
Soda cleaning
Cleaning process:
- Preliminary Test: Ravol test to determine depletion values.
- Protection: before cleaning, cover the shaft ends and glue them so that the bearings are not damaged.
- Cleaning: a high-pressure roller saves the cups 4 times back and forth, removes dried dirt from the cups using a baking soda vacuum and even out the surface tension of the raster cylinder, at the end of the process the baking soda is removed with water.
- Result: Another Ravol test can be used to determine the extent of the change. The result of this is attached to the customer so that he is properly informed about the condition of his cylinder (before / after).
Laserclean version
Cleaning process:
- Using the Dotscope scan, a 3D micro image is taken of the surface of the cylinder.
- The rollers are cleaned either online or offline at the printing press.
- Cleaning can be 1-2-3x rounds, depending on the cleanliness of the drum
- The cleaned cylinder is measured again and the customer receives a report on-line
- The cylinder is audited and received by the printer to know the condition of the cylinder.
Quality department
- Density test
- Water content measurement
- Refractive index measurement
- GC test
Density test: performed with a metal pycnometer, a measure of the mass of a given unit of volume.
Water content measurement: for the determination of a test substance of known mass, from an automatic burette, the instrument is dripped with Karl Fischer reagent with constant stirring until the iodine color of the iodine remains dark brown.
Refractive index: The refractive index is examined with an Abbe refractometer. The refractive index is based on the principle of refraction.
GC Assay: Gas chromatography is a gas-liquid separation process in which mixtures are separated into components.
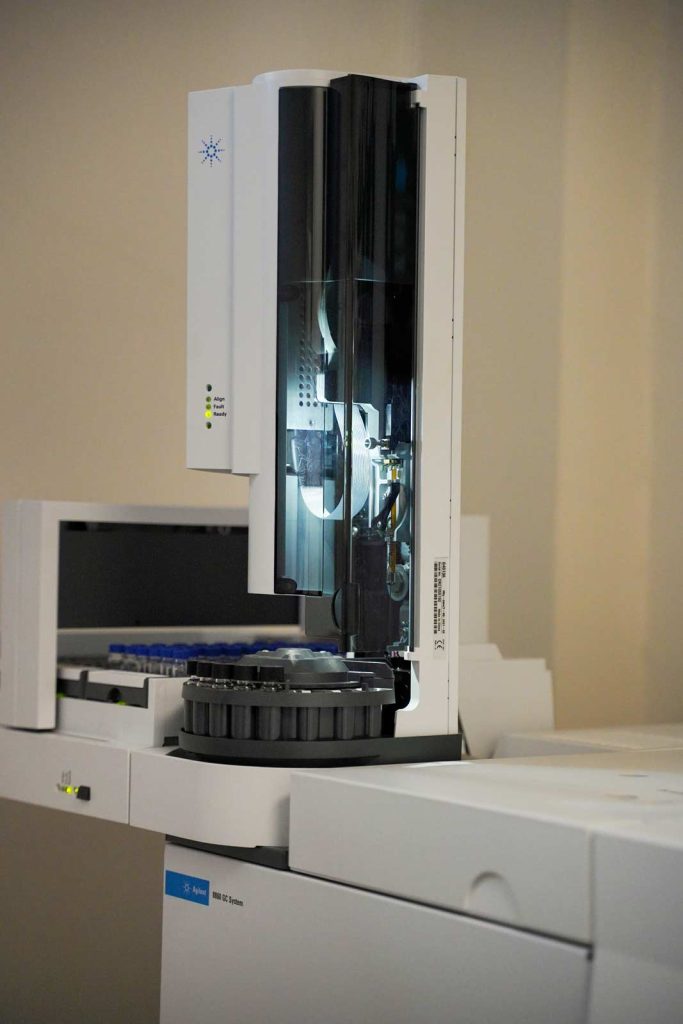
Paints test
- Appearance
- Density test
- Non-volatile matter content test
- Drain time determination
- Determination of grain fineness
- Wet coverage
- Drying
Leakage time determination: during the measurement, the time during which the 20oC material flows out of the metal cup filled to the color through the appropriate opening (4 mm and 6 mm) is determined.
Opacity test: the test is performed with a cryptometer. Multiply the reading on the base plate scale by the density of the material and the value on the cover plate.
Rubbing fineness: the grain fineness is done with a grindometer. The abrasion fineness is the maximum particle size in microns of a pigment present in a given dye suspension.
Drying time test: the drying ability is a very important property of the paint. The use of fast-drying paint shortens the painting time, reduces the painting costs and the disturbing effects associated with painting (dusting, adhesion of foreign substances).
Determination of non-volatile matter content: this test is carried out in an oven. The dry matter content is the fraction of the test substance obtained after removal of moisture (solvent). The dry matter content is given as a percentage by weight.
Color test: Performs with a Gretage type colorimeter. Based on the Pantone card, the device determines the desired color. The machine offers the possibility to mix the color requested by the customer from the colors in our concentrate system.
Ink mixing
Flexo
- Water
- Solvent
- UV
- LED
Offset
- Traditional
- UV
- LED
The goal of our ink kitchen is to enable our printing partners to work quickly and with the right quality. In addition to mixing individual colors, we perform material tests, color adjustments and print tests here.
We have a separate mixing system for each printing area, and we also provide a separate room for mixing LM (low-migration) inks.
Our specialists can make up to 1 kg of paint. If you have trouble printing, send us a sample of the media and our colleagues will try to provide a suggestion as soon as possible.
All types of additives from our printing industry suppliers can be found in the paint laboratory of CNI Ltd. Additional additives are important during printing, as we come across different systems for each printer. Through the universal adjustment of paints, errors and obstacles constantly occur in the case of individual systems.
The source of the questions can be many things, raw material, drying system, paint and varnish, or a different combination of these that is not appropriate. The biggest concern is that all manufacturers are trying to comply with EU standards, which are becoming stricter year by year, forcing them to lack well-functioning ingredients in their products.
Practice shows that the printing industry suppliers (CNI Kft.) And the printing houses, as the end user, usually do not receive information about these changes. Experienced product solutions that work well therefore need to be reworked often, depending on the project, even several times a year to adapt the product to market expectations. It is the task of our inkjet kitchen and the staff working there to quickly and efficiently test the raw material you want to print, to create a new recipe for the customer with the right additives, thus providing a solution to the everyday quality requirements of the printing house.
- Raw material
- Technology
- Color code, measurement result, LAB value
- Application rate g / m2 (Flexo: anilox)
- The question of varnishing
- Speed
- Other product requirements